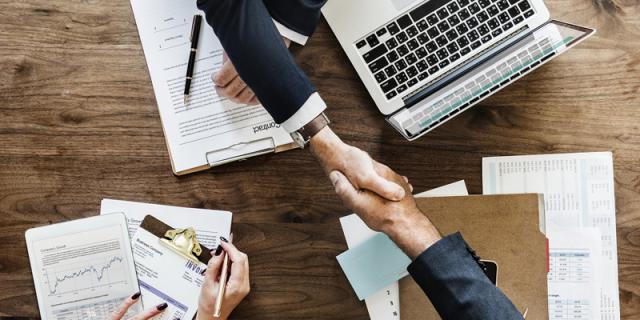

1. Safety and health
Continuous improvement of safety
- To reduce drastically the plenty of accidents.
- To develop a practice of prevention.
- To advance the ergonomics of the workplace.
- To develop specific professional talents.
2. Cost Deployment
Investigation of the losses and costs
- To identify scientifically and systematically the principal items of loss in the system production logistics market.
- To quantify the inherent economic privileges and expected.
- To address the resources and commitment to managerial tasks with the greatest potential.
3. Focused Improvement
Priorities of actions to management
- The loss identified by the cost deployment
- To overcome drastically the most important losses present in the system manufacturing plant, eliminating inefficiencies.
- To eliminate non-value-added activities, in order to strengthen the competitiveness of the cost of the product.
- To develop specific professional skills in problem-solving.
4. Autonomous Activities
Continuous improvement of plant and workplace
It contains two sub-pillars-
- Autonomous Maintenance: It is used to improve the overall productivity of the production system through maintenance plans through the engineers.
- Workplace Organization: It is developed to manage an improvement in the workplace, because often the materials and equipment are degraded; in particular because in the process there are many losses to remove.
5. professional maintenance
Continuous improvement of downtime and failures
- To increase the efficiency of the machines using failure analysis techniques.
- To facilitate the collaboration between engineers and maintainers to reach zero failures.
6. Quality Control
Continuous
improvement of
customers’ needs
- To ensure quality products.
- To reduce non-compliance.
- To increase the skills of the employees.
7. Logistics & Customer Service
Optimization of
stocks
- To reduce significantly the levels of stocks.
- To minimize material handling, even with direct deliveries from suppliers to the assembly line.
8. Early Equipment Management
Optimization of
installation time
and costs and
optimization
- To put in place new plants as scheduled.
- To ensure a rapid start-up and stable.
- To reduce the Life Cycle Cost (LCC).
- To design systems easily maintained and inspected.
8. People Development
Continuous
improvement of the
skills of employees
and workers
- To ensure, through a structured system of training, suitable skills and capabilities for each workstation.
- To develop the roles of maintenance workers, technologists, professionals such as significant staff training.
10. Environment & Energy
Continuous
improvement
environmental
management and
reduce energy waste
- To comply with the requirements and standards of environmental management.
- To develop an energy culture and to reduce the energy costs and losses.
0 Comments
Thank for Visiting our site
we will Happy to see you here again